|
|
|
We produces a wide range of optically clear (ITO PET) Indium Tin Oxide coated transparent, conductive film products.
ITO PET products are produced by vacuum sputter deposition of ITO, a process that affords excellent coating uniformity and adhesion.
All standard our ITO PET products are produced on optical grade polyester film. By special order ITO coatings are available on other film
substrates, for example, heat stabalised film, anti glare film, or clear hard coated polyester film. Also by special order, we offer ITO coatings
with a surface resistance that is higher than that of standard ITO PET products.
|
Application |
Structure |
- Touch screens components
- Electroluminescent (EL) lamps
- Transparent Heating Elements
- Electrophoretic displays
- Sensors position
- Liquid crystal devices
- Membrane Switches
- EMI shielding
- Smart windows |
Transparent Electroconductive Film
 |
ITO (Indium - Tin Oxide) |
 |
PET Film 125µm (+/-5) |
|
|
|
Item |
Unit |
NOK 100HA-125A |
Test Method |
Thickness |
|
µm |
125µm (+/-5) |
Micrometer |
Width |
|
MM |
1000mm (+/-2) |
Measurement Tape |
Length |
|
M |
100m, 500m |
Measurement Tape |
Base Film Quality |
Transmittance |
|
% |
≤89 |
ASTM D1003 |
Haze |
|
% |
1.5 (+/-1) |
ASTM D1003 |
Thermal |
MD |
% |
≤1.2 |
JIS C2318:1997 |
Shrinkage |
TD |
% |
≤1.2 |
JIS C2318:1997 |
Hard Coat Hardness |
|
H |
 - |
JIS K5400 |
Specification |
Surface Resistance |
|
Ω/sq. |
90 (+/-20) |
4cmx4cm, 3 point average |
|
|
|
|
Parallel Elctrode |
Transmittance |
|
% |
≥ 75 |
ASTM D1003 (550nm) |
Haze |
|
% |
1.5 (+/-1) |
ASTM D1003 |
ITO Adhesion |
|
% |
100 / 100 |
Cross cut test JIS K5400 |
Thermal |
MD |
% |
≤1.2 |
JIS C2318:1997 |
Shrinkage |
TD |
% |
≤1.2 |
150°Cx30min. |
Environmental Character |
High Temperature Test |
|
R/Ro |
1.0 (+/-0.25) |
150°Cx60min. |
High Temperature Storage |
R/Ro |
1.0 (+/-0.25) |
80°Cx250hrs |
High Temperature Moisture |
R/Ro |
1.0 (+/-0.25) |
60°Cx95%RH x 250hrs |
Chemical Character |
Ethanol |
|
R/Ro |
1.0 (+/-0.25) |
R.T 30 min |
Acetone |
|
R/Ro |
1.0 (+/-0.25) |
R.T 30 min |
Toluene |
|
R/Ro |
1.0 (+/-0.25) |
R.T 30 min |
|
SAppearance |
Scratch / Linear Defects |
Method |
Size |
Length |
Spec. |
Remark |
Visual Inspection |
W > 0.05mm |
L > 2mm |
NG |
In case scratch / smudge are more |
0.02 < W≤0.05mm |
L≤2mm |
≤20 |
than 2, distance between the 2 |
W≤0.02mm |
|
OK |
should not be less than 10mm/m2 |
Particle, Bubble, Smudge |
Method |
Size |
Length |
Spec. |
Remark |
Visual Inspection |
0.3mm < Ø |
 - |
NG |
Not exceed m2 (black spot, white |
0.2mm <  ØÂ ≤0.3mm |
 - |
≤10 |
spot, sparkling spot, ITO coating |
Ø â‰¤ 0.2mm |
 - |
OK |
peeling off. |
Visual Inspection |
Dimp, Dent, Hole |
|
Particle size Ø = (a + b) / 2 |  | |
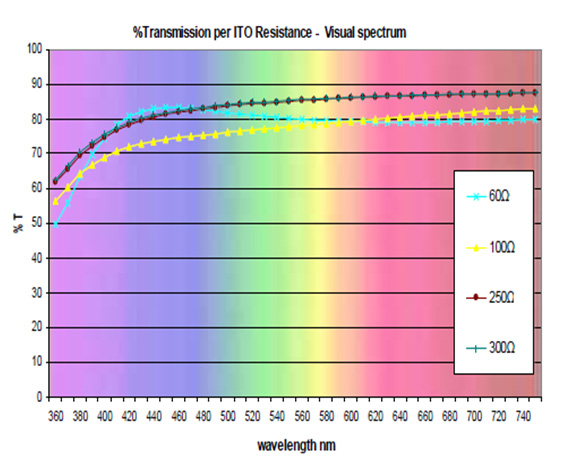 |
Electrical Uniformity |
All products feature electrical uniformity of 10% within any one square foot
area, defined as the maximum difference from the average ohms per
square value within that area. However, touch screen manufacturers
typically achieve < 1% resistance linearity by orienting their sensors
(busbars) so that the electrical current path is always in the direction
of the length of the film roll.
|
Handling |
Vacuum deposited ITO coatings are very thin and are easily scratched or cracked if handled improperly. When removing film from a roll, care should be
taken not to bend or crease it. It is important never to allow the ITO coated side to come in contact with a surface, such as a table, during processing
operations. Sliding ITO coating over a surface will scratch the coating, resulting in elevated surface resistance and visible defects.
Please note that all ITO PET film product supplied in sheet form is supplied with protective liner on all surfaces.
|
|
|
|
|
|